by Codey Henderson, Ph.D. and Camden Henderson, PhDGarnet Solutions Group
Lithium-ion batteries continue to become more prevalent in today’s marketplace. Unfortunately, as the batteries age and their construction materials degrade, cracks can form in their coatings, or internal components can short and lead to a fire. The actual chemical reaction that causes the fire can end after a short time, depending on the size of the battery and severity of the failure; however, the chemical fire may ignite nearby combustible material and can cause a more involved fire.
Many times, old batteries are not stored properly. In one case, a stack of old lithium batteries was piled on top of each other waiting for disposal when they caught fire. This fire caused damage to the structure, equipment, and general contents. An industrial hygienist (IH) was brought in to determine the appropriate protocol for remediation and worker safety. The IH inspected the loss site, took air samples, and had the air sample analyzed for lithium and other contaminants that would be harmful to the employees cleaning up after the fire. The results of the air sampling did not reveal any lithium or other air-borne contaminants that would have been harmful to the mitigation workers. The cleaning protocol which was then written required all the employees to wear full PPE (Personal Protection Equipment), vastly increasing the labor, time, expertise, and ultimately the cost required to mitigate the damage and restore the facility and equipment following the loss. The IH did not take any wipe samples to determine that any by-products of the batteries were left behind by the fire. This information would have been very helpful to have prior to writing the personal protection plan, as it would dictate the actual hazards and necessary precautions. The IH wrote a protocol that assumed maximum hazards even though it was unsupported by the data.
So how should a lithium-ion battery fire be handled? First, we should understand more about the battery, how and why it burns, and what combustion bi-products we should be looking for.
Lithium-ion battery technology is relatively young, but the batteries have undergone significant changes, upgrades, and adaptations since their appearance in the market. As such, there are variations in the materials and chemicals involved, but the basic components remain the same and are shown in the image below with some of the more common materials.
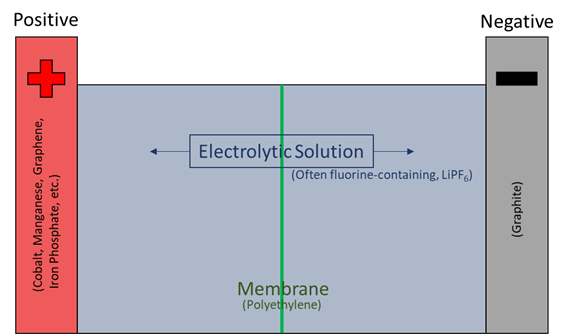
In general, a lithium-ion battery has a carbon-based negative electrode, a metal-oxide positive electrode, a separating membrane, and an electrolyte composed of lithium and an organic solvent. The battery components are part of a sealed container to prevent contact and reaction with the air, as lithium is highly reactive with moisture.
The membrane separating the positive and negative terminals may be only 15 microns thick (about 0.0006 inches). When either the battery is ruptured or the membrane fails, the battery can generate excessive heat and catch fire as either the lithium ions react with the moisture in the air or the battery shorts. Additionally, the electrolyte will break down at temperatures above 275 °F and generate additional heat thereby further complicating the fire.
In the loss mentioned above, the rupture of the first battery initiated the fire and quickly caused the rest of the battery stack and other combustibles in the area to ignite. What bi-products might we expect to see based on our knowledge of the battery composition? The carbon and metal oxide terminals may produce carbon-based residue similar to a “normal” fire if the fire is sufficiently intense. The hydrocarbon-based container and membrane may produce bi-products comparable to burning plastics, which may produce corrosive anions. As many electrolytes contain lithium and fluorine-containing salt, the electrolyte will likely combust to produce a form of lithium and fluorine, which are highly reactive (meaning that they will rapidly react to form a stable compound). The fluorine may be any number of corrosive species, including fluorine gas (F2).
As each loss is unique, it is important to understand the contaminants, the hazards, and the appropriate sample analysis. So now that we know what contaminants to expect from the lithium battery fire, how should we test for them? Surface sampling is necessary to collect soot, ash, and other burn residues from the structure and equipment in the contaminated areas in question. It is important to then work directly with a laboratory to identify the contaminants in the area affected by the fire and/or soot.
In a “normal” fire, the wipe samples should be analyzed for corrosive anions and cations. In many cases, the list of anions or cations is limited based on the type of fire and what was burned; in the case of a lithium battery fire, you would need to expand the list of analytes that are being tested to address the unusual potential hazards. The most common anions that are tested for following a fire are chlorides, nitrates, and sulfates. Many laboratories use ion chromatography to do the testing and can report additional ions of interest. Based on our knowledge of the lithium battery and its combustion bi-products, you should request that the testing analyze the samples similarly to a normal fire and include fluorine and lithium in the testing protocol. It should be noted that the laboratory doing the testing can report to you any other unusually high anions that they might discover during the running of the samples. Both fluorine and lithium are expected to react rapidly; however, they should still be tested for in wipe samples to determine the extent of the fire and ensure they are no longer a hazard to equipment, structure, or workers.
Based on the scientific testing results, a proper protocol can then be written, detailing cleaning protocol, worker health and safety, and equipment restoration. Without such testing and understanding, we risk not only taking unnecessary precautions, we risk NOT taking the right precautions to properly address the hazards and uniqueness of each loss.
If you would like more information about this subject, please contact the author, Codey Henderson at 470.552.2663 or codey.henderson@garnetsg.com.
This is a publication of Southern Loss Association, Inc., P.O. Box 421564, Atlanta, GA 30342. The articles published on this website are in a general format and are not intended to be legal advice applicable to any specific circumstances. Legal opinions may vary when based on subtle factual differences. All rights reserved.